Plant instrumentation and controls: Issues and drivers
Instrumentation and controls (I&C) operators are dealing with aging equipment that doesn’t allow them to take advantage of modern technology’s benefits, which can give them access to real-time information that allows them to make better decisions.
Learning Objectives
- Instrumentation & controls (I&C) modernization projects are often considered infrastructure projects.
- Three modernization drives are obsolescence, regulatory compliance and digital transformation.
- Advanced process control (APC) is an example of technology end users can justify with proven return on investment (ROI).
The needs of today’s business world are dynamic. The ways we communicate, inform, collect data, analyze and report have gone through many changes. Now, the pace is accelerating. Operators are asking whether it is time to update the technology or face the consequences of falling behind.
Industrial plant operators should keep from falling behind. Running a plant with aging instrumentation and controls (I&C) presents a major challenge for plant management. Operators face various age-related issues such sensors out of calibration, blocked impulse lines, spurious shutdowns, seized valves, and failed actuators. The result is the reliability of the system is uncertain and plant safety is at stake.
Furthermore, aging instrumentation and control systems are likely to present problems as the company undergoes a digital transformation. The older platforms are not only unable to provide the increased data a digitally transformed enterprise expects, but they may not even be able to communicate in the new business environment. In addition, since no system today is secure through obscurity, it could present cybersecurity risks.
As illustrated in Figure 1, several questions come to mind. For instance, is it worth the cost to continue to operate and maintain the aging system? What are the benefits and added value of a new system? Even more serious is whether the existing system is safe to continue operating.

Figure 1: Questions that come to mind when considering instrumentation and control (I&C) system modernization. Courtesy: Yokogawa
I&C modernization possibilities
I&C modernization projects are generally considered infrastructure projects. A tendency is to simply scope the distributed control system (DCS) while overlooking other risks or issues with connected equipment, which could also be obsolete. Many managers view the modernization project as a purely defensive move. The main objective is to overcome the failings of the older system or instruments but otherwise keep the unit or plant exactly as it has been.
Such a “like-for-like” approach can be successful if the only desired outcome is recreating the status quo. Many projects are designed along those lines. The problem with this approach is a major lost opportunity. Once again, it could impede digital transformation and present cybersecurity risks. It could also make it difficult to upgrade technology or transition to open architecture in the future.
Such a project is a major undertaking and can only be successful if addressed with careful planning. In the end, the risks of an unsuccessful project are serious. Costs can spiral out of control and production can be disrupted. Poorly configured systems or instruments can have trouble controlling the process. On the other hand, when planned well, a modernization project, even a large-scale system migration, can move from phase to phase on time and within budget, resulting in significant operational improvements.
Three modernization drivers
It is remarkable many DCS platforms, which were designed and installed in the 1970s and 1980s, have provided outstanding longevity. Unfortunately, these systems are showing their age. In many cases, much of the equipment needs to be upgraded or perhaps undergo a full migration to a new DCS and modernizing the plant.
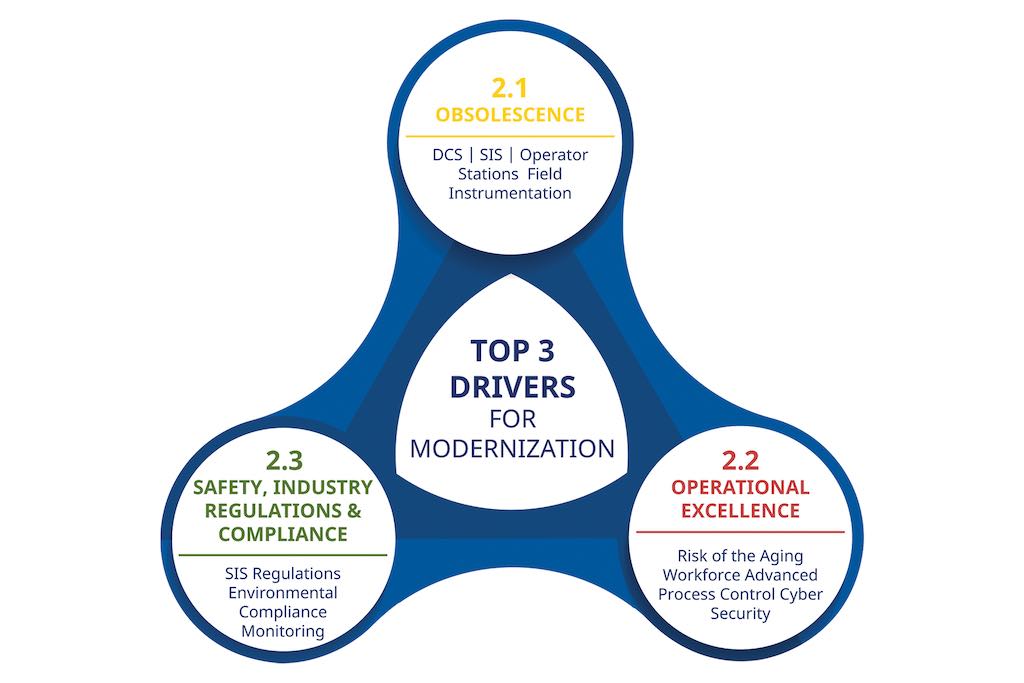
Figure 2: The top three drivers for I&C modernization. Courtesy: Yokogawa
What drives plant modernization? These three challenges are the biggest reasons for plant modernization projects:
- Obsolescence
- Regulatory compliance; health, safety and environmental (HSE) issues
- Digital transformation/transformation to operational excellence
1. Obsolescence
Operating a plant with aging instrumentation and controls creates several potential problems for operators and the production process. In addition to the age-related issues cited earlier, the documentation for most control systems including process and instrumentation diagrams (P&IDs), control narratives, strategies, and control system utilization is likely not up to date. It’s also likely the company lacks a complete spare parts inventory, with some parts no longer available. Old control system platforms and instrumentation increase the risk of failure and production interruptions. They also lack many of the capabilities of newer systems for improving plant performance.

Figure 3: Typical plant and equipment lifecycles. Courtesy: Yokogawa
The obsolescence dilemma
According to ARC Advisory Group, failure rate data for automation systems is not precise and supporting information presents a wide range of actual failure rate experiences. In many plants users do keep track of failures, but the failure analysis is not sufficient to help predict end-of-life accurately. By observing the theoretical “bathtub curve” chart originated by NASA (please refer to Figure 4), the question arises whether it is a valid analysis. For many automations systems, the time along the x-axis ends up in a range of between 15 and 50 years. The lack of precision in determining asset end-of-life make decisions around this important area difficult.
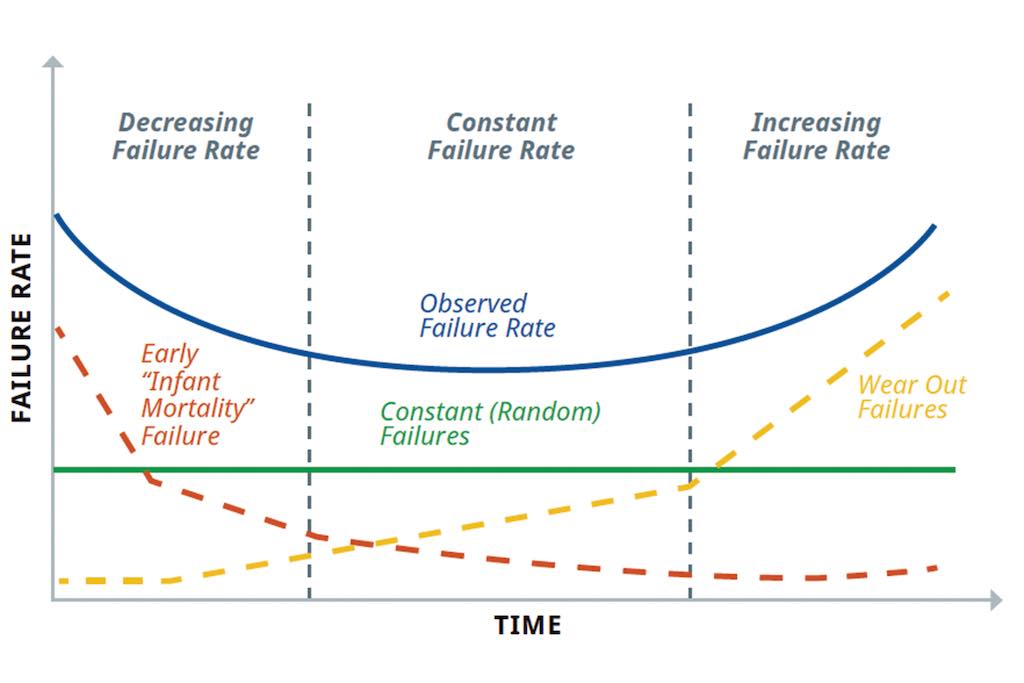
Figure 4: The “bathtub curve” hazard function (blue, upper solid line) is a combination of a decreasing hazard of early failure (red dotted line) and an increasing hazard of wear-out failure (yellow dotted line), plus some constant hazard of random failure (green, lower solid line). This curve is widely used in reliability engineering and it describes a particular form of the hazard function. Courtesy: Yokogawa
2. Regulatory compliance; health, safety and environmental (HSE) issues
In today’s industrial manufacturing operations, there is increased emphasis on health, safety, and the environment. Unfortunately, accidents continue to occur in many facilities even after the installation of safety systems and other precautions initially considered adequate.
Over the past 25+ years, the process industry has witnessed a continual evolution of process safety standards. The main intent of these industry standards is to provide guidance and best practices to manage the inherent risks associated with the manufacture and handling of chemicals, hydrocarbons, and other hazardous materials. In 2018, the North American and international versions converged to create the ANSI/ISA-61511-2018 / IEC 61511:2016, Functional Safety – Safety Instrumented Systems for the Process Industry Sector. This standard is now the primary driving force, globally, behind the work processes to design, implement, operate, and maintain safety instrumented systems.
3. Digital transformation/transformation to operational excellence
According to ARC Advisory Group, for many plant owners, obsolescence alone cannot justify the execution of a large capital upgrade project. Instead, enhanced functionality and system performance to improve operational excellence are major criteria impacting funding decisions.
Eight issues, risks and opportunities as drivers
Enhanced functionality is the concept of a plant of factory’s capability to implement the latest technologies and innovations to deal with a wide range of challenges in a certain industry related to technology. To deal with these challenges in the future, new technologies or innovations might be necessary. If the installed base of instrumentation and systems cannot support new technologies, an upgrade or even a complete replacement could be required. In such a case, these “platforms for the future” could trigger plant modernization.
1. Cybersecurity
The continuous evolution of the control system has enabled organizations to protect the investment in equipment and control strategies over long periods of time. However, interfacing decades-old controllers with current technology also makes this equipment indirectly vulnerable to attack. All these systems have one common denominator: they experience gaps in support. This makes them more vulnerable than contemporary systems.
Modern systems support new cybersecurity approaches, which often transcend budgeting cycles due to their coincidence with industrial asset insurance, HSE, and disaster recovery strategies. The cybersecurity strategy has transitioned from a problem to fix to a risk to manage. When businesses look at cybersecurity in this manner, it removes the mystery and becomes an issue upon which management can act.
New I&C systems accommodate the evolving cybersecurity landscape in which threats continue to change. No longer distracted by technological issues, management can focus on risks.
2. The evolving workforce
Finding experienced personnel is already a major challenge for the process industries. An executive at a major refining company stated his company lost 2500 years of experience when 100 operators retired.
Research has shown the largest reason for unscheduled downtime is operational or human error, which accounts for 42% of the unscheduled shutdowns in the process industries. However, there are ways to assist operators in making the best decisions at times of increased stress such as during start-up, transitions, or upon the occurrence of abnormal conditions. With increased emphasis on personal safety, performance management, continuous improvement and training, companies are investing in their people and are eager to apply emerging technologies.
3. Control room design
An appropriately designed control room will make people feel relaxed and secure. As a result, operators and managers can fully concentrate on plant operations and stability. Improvements in data integrity and data availability accelerate communication between units to optimize the total operation.
4. Modular procedural automation
There are many more benefits to deployment of ISA TR106, Modular Procedural Automation (MPA), than would meet the eye. MPA digitalizes standard operating procedures, which are critical to achieving safety and efficiency. MPA helps ensure the know-how of experienced operators is maintained in the procedure flows and provides new operators opportunities to learn more about the process. KPIs accomplished could include significant reductions in the number of operator actions, number of alarms handled per operator, and time-to-stability during transitions in the process.
In addition, the digitalized procedures could be supplemented with a digital twin. The digital twin emulates the human operator in real time and incorporates deep knowledge of the process, standard operating procedures, and human behavior across many situations. Advanced decision support allows testing of “what if?” and “what’s best?” scenarios to determine available strategies that not only improve human operator performance but improve quality, safety, process uptime and process performance, as well.

Figure 5: MPA combines the best procedures from all operators into a best-practice standard operating procedure. Courtesy: Yokogawa
Companies whose process control systems use a significant number of manual operator procedures can also use the digital twin as a springboard from semi-automated operations to fully autonomous operations. Since the MPA solution could be used in conjunction with the existing system, it provides flexibility to the modernization project.
5. Human-machine interfaces (HMIs)
Safe and efficient operations rely on the ability of the operations staff to quickly identify potential process deviations before the situation reaches an unsafe or undesirable production condition.
Modern HMIs provide compliance with Abnormal Situation Management (ASM) Consortium recommendations including a standardized symbol library, which clarifies process operations. Modern HMIs support features today’s mobile device users expect such as augmented reality and virtual reality (AR/VR) functions, which enhance the operator experience.
Today’s systems also fully support autonomous remote operations. Although much of this functionality was available prior to the COVID-19 outbreak, the pandemic expedited end user acceptance. In contemporary manufacturing, operators and technicians need not be located physically on-site.
6. Operator training system (OTS)
Given the challenge presented by the retirement of many operators, especially those who are familiar with efficient and safe operations, early training of new operators and successful knowledge transfer from more experienced operators has become critical.
Today’s process simulators provide excellent solutions by depicting actual process operations, including problem and anomaly scenarios. The simulators improve the quality of operator responses and timeliness of actions taken in response to process upsets and incidents. If a digital twin is used in conjunction with the OTS, it can be regularly updated with actual events.
7. Alarm management
Modernization projects often present excellent opportunities to boost alarm management quality and effectiveness. Alarm management and alarm system rationalization can substantially reduce the number of alarms to which operators must react. By preventing operator overload, they ensure appropriate and timely reactions to important alarms.
8. Collaborative mobile robots
Despite these advances, manufacturers continue to experience staffing difficulties. At the same time, concerns about staff well-being and personal safety are increasing. Collaborative mobile robots represent an emerging solution. In place of human operators or technicians, the robots can venture into hazardous areas for inspection rounds. Drones can operate in situations where heights present hazards. Today’s audio-visual and sensing technologies can emulate human sensing in a manner that makes the robots effective.
Advanced technology benefits for I&C projects
Contemporary systems make it easier to inject new technologies such as artificial intelligence and digital twins into the architecture. Advanced process control (APC) is one example of a technology end-users can justify with a proven return-on-investment (ROI) track record.
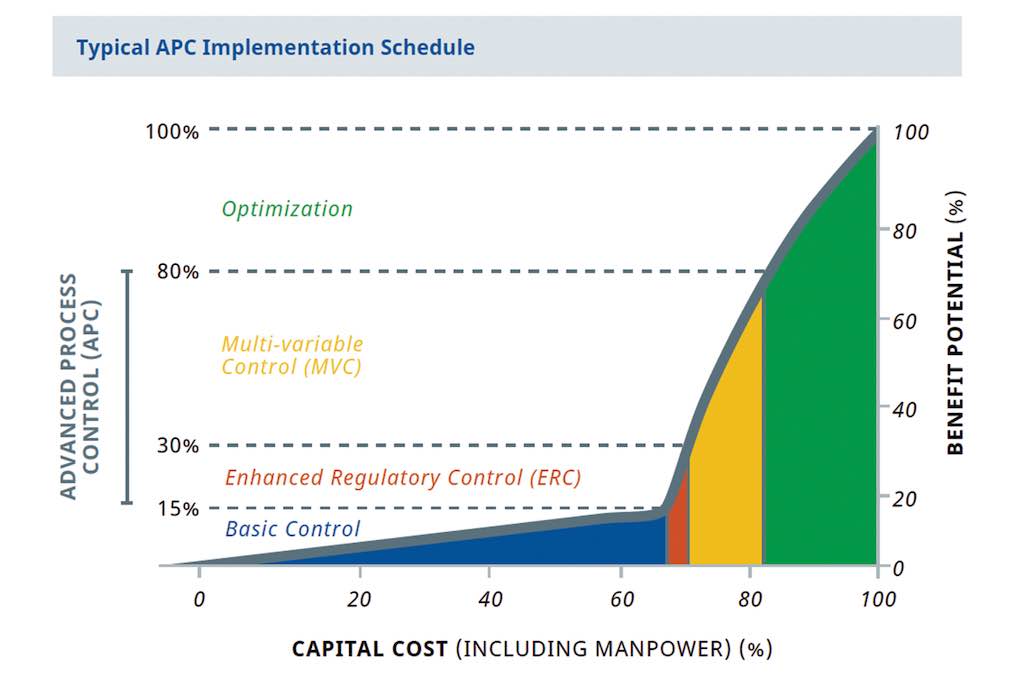
Figure 6: APC cost vs. benefits. Courtesy: Yokogawa
By now, since virtually every industrial process in the world is under automatic control, APC is the logical next step. APC has already been implemented in many facilities with varying degrees of success. Today, APC subject matter experts have learned how to produce solid results.
Multi-variable control (MVC) is the key component of an APC platform. It enables optimum process stabilization and results in increased productivity. MVC achieves this by predictive control using process dynamic models, which are proving to increase throughput, conserve energy, and reduce quality giveaway.
Today’s more user-friendly advanced control and real-time optimization tools are playing a larger role in maintaining profitable, competitive operations. APC solutions provide many advantages for the process units, such as:
- Improved process yields
- Increased throughput
- Reduced energy consumption
- Improved process stability
Operational improvements such as those shown in Figure 6 can trigger plant modernization and are often used to justify the costs.
Benefits of upgrading
Since the pace of technological advancements has been accelerating, plant operators are finding it more difficult to justify the maintenance of aging or obsolete instrumentation and control (I&C) systems. While many systems have worked more reliably and have lasted much longer than expected, today, they present too many risks. Those include not only cybersecurity, but emerging expectations in terms of health, safety, and environmental (HSE) issues and sustainability.

Figure 7: APC return-on-investment in terms of benefits per year. Courtesy: Yokogawa
New demands such as support of digital transformations and initiatives that address emerging needs of the evolving workforce allow management to justify an investment in I&C modernization. If the new system enables the deployment of technology such as advanced process control (APC), the resulting operational improvements can be used to justify the costs.
Kevin Finnan, advisor, market intelligence and strategy, Yokogawa. Edited by Chris Vavra, web content manager, Control Engineering, CFE Media and Technology, cvavra@cfemedia.com.
MORE ANSWERS
Keywords: process instrumentation, instrumentation and controls
Do you have experience and expertise with the topics mentioned in this content? You should consider contributing to our CFE Media editorial team and getting the recognition you and your company deserve. Click here to start this process.